
Process
We take projects from conception to completion in a single 77,000-square-foot facility devoted entirely to pushing the boundaries of public art and interactive exhibits.
Since we are there every step of the way, we can test ideas extensively during the design process and can respond quickly to whatever obstacles or opportunities arise during fabrication. With comprehensive resources under one roof and deep connections to our community, we extend a consistency of vision to all aspects of a project.
Concept
Development
Our process begins with brainstorming and discussion about the goals for a project. These goals get translated into themes and quickly become sketches on the whiteboard.
At the end of the brainstorming process, winning concepts are selected and handed off to an experienced designer.


Design
Designers transform concepts into fully realized sophisticated designs. Our design process includes modeling the concepts in various software platforms, breaking the design into parts, and figuring out how to fabricate it.
As designers develop these details they collaborate with other team members to discuss the needs of the project. Since most of our designs combine different media, designers consult with our electronics and fabrication teams to design the most compelling project possible. Once we have a viable approach, the designer works alongside a fabricator for prototyping.
Prototyping
Designers work with skilled structural and electronics fabricators to mock up nearly all of our projects. Whether it is testing a sculpture’s structural capacity, experimenting with new fabrication processes or testing interactive lighting effects, prototyping takes the design from the digital realm into reality.
During the prototyping phase, our team works through an iterative process of testing and evaluating the design. We often invite people to Creative Machines to test our prototypes so we get a true sense of how the public will interact with the project. Once the design has been vetted, the designer continues detailing the project and fabrication begins.
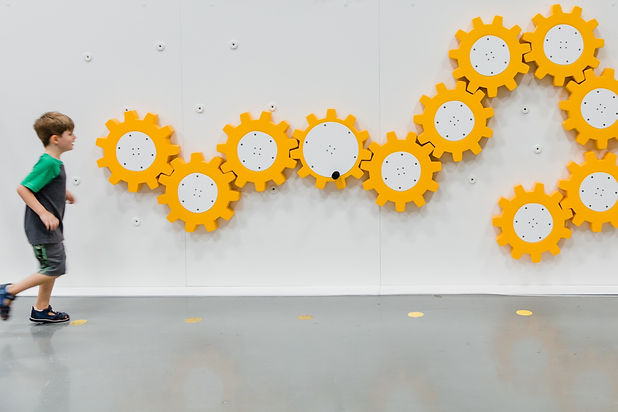
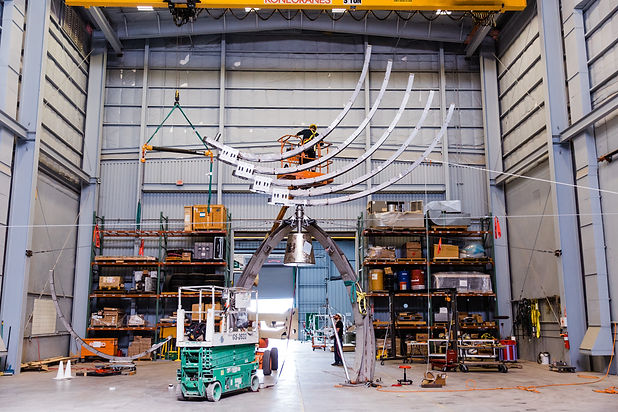
Fabrication
Fabrication begins with the proper selection of fabrication team members based on their specialized skill sets and availability. The Fabrication Manager sets up a schedule for the project and works closely with the designer to resolve problems and ensure accuracy during fabrication.
Fabrication timelines vary and are dependent on the installation deadline and the project’s complexity. All projects are built, assembled, and tested in our shop. Fabrication is complete when the project passes a final quality assurance review. Then, it is disassembled and packed for shipping.
Shipping +
Installation
The project manager is primarily in charge of shipping and works with the design and fabrication team to get accurate dimensions and weights for each part. We build custom crates for our projects and take extra care when packing each item to protect it during transit. We have extensive experience shipping projects that come in all shapes and sizes within the US and to countries around the world.
​
Prior to on-site installation, we create a detailed installation plan reviewing every detail to ensure a smooth and efficient installation. The team travels to the site and typically meets the trucks to unload the shipment. They carefully install the project making sure that it is properly integrated into the site and in pristine condition. Finally, the team tests all aspects of the project and cleans the site.
Following installation, Creative Machines compiles a manual pulling all details of the project together in one place and outlining maintenance procedures.
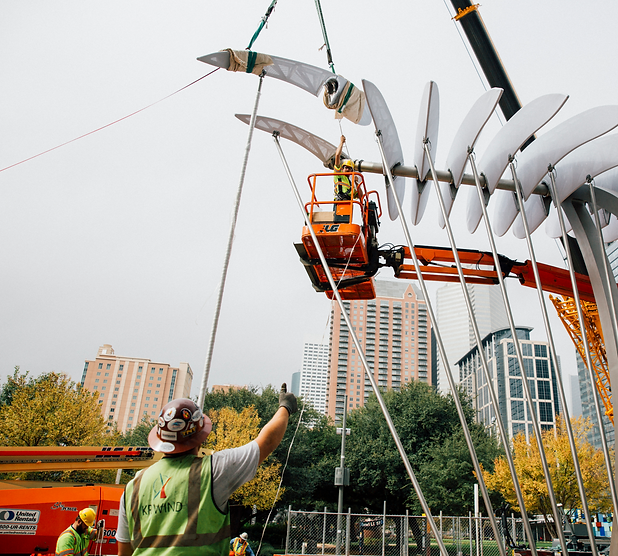
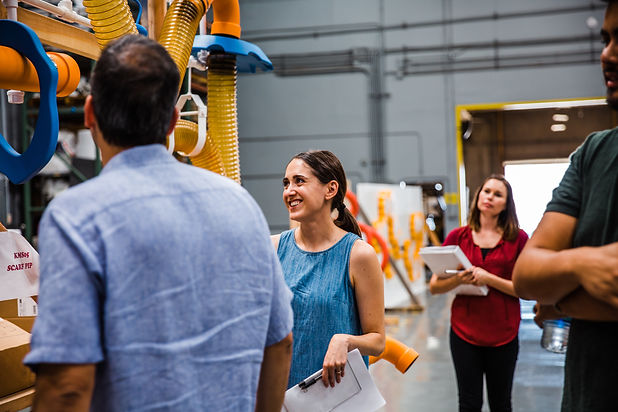
Aftercare +
Warranty
Creative Machines is known for its dedication to clients throughout the warranty period and beyond. Once you start a project with us, you get lifetime support.